After the definition of what is a die cutting machine? And the benefits that the die cutting machine brings, but the operating mechanism of the die cutting machine is still making people wonder how it works?
For manual die-cutting machines, a piece of paper is placed on the base of the machine. As the platform passes through the machine, uniformly distributed pressure is applied to the mat, pressing the metal mold into the paper. Next, the sharp edges of the die will create the shape you want. But if you are a beginner in using die cutters or electronic cutters. Surely this article will explain and provide some introduction to die cutting.
1. What is die cutting?
Die cutting is a process that uses specialized machines and tools to transform raw materials by cutting, then shaping and trimming materials into shapes and designs according to the size and shape look I want.
In general, both are flexible and can be adjusted according to the level of forming, and the die cutting process is suitable for almost all materials such as metal, plastic, wood and composites. The die cutting also has manufacturing applications that cover a wide range of industries including die cutting synthetic resins, gas marketing, die cutting paper, packaging, die cutting fabric and die cutting foam manufacturing.
In addition, flat, rotary and semi-rotary die cutters are known as industrial-scale die cutters, with a thicker and harder surface design to accommodate parts with revolving speeds. In contrast, for manual and digital die-cutting devices, they are mostly used for simple parts and accessories.
2. How does die cutting work?
There are actually several different types of die cutting processes including flat die cutting, rotary die cutting and digital die cutting, with each process having its pros and cons from requirements and specifications by an application. specific die cutting application.
To prepare for cutting it is necessary to prepare the converted material, part dimensions, tolerances, start-up costs and long-term, cutting time. This helps you determine the right type of die cutting process to use in a variety of purposes.
3. Types of die cutting
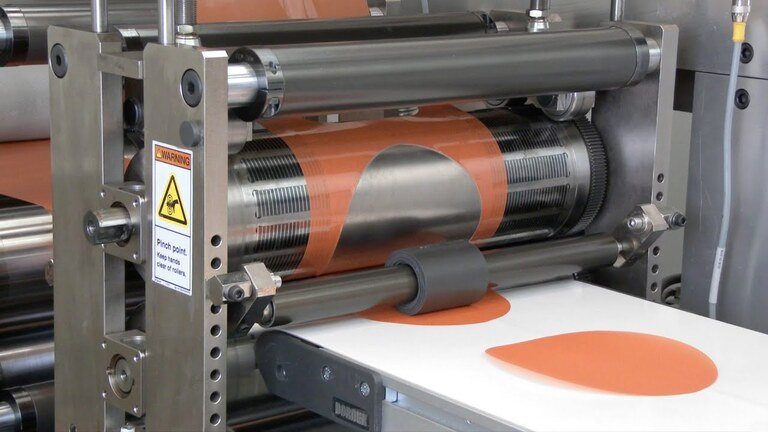
As mentioned above, there are several types of die cutting such as flat die cutting, rotary die cutting and digital die cutting. Each will have processes that provide pros and cons to manufacturing applications, as well as limitations related to material capabilities, tolerances, production output, cost, and more.
Flat die cutting, also known as steel rule cutting, is known to be a manufacturing process that uses a flat die cutting press and a custom steel rule die to cut materials into other shapes and designs together. This die-cutting process is suitable for processing thicker materials, large-scale production of larger parts, and means short single completion times.
Rotary die cutting is known for the process of using cylindrical dies attached to a rotary press for flexible material transformation (wed). They are ideal for application in high-precision designs and high-volume production operations.
Digital die cutting is also a material conversion fabrication process that does not require the use of a mold. In contrast, they will use lasers, blades, and computer-controlled tools to create cuts, marks, and wrinkles. This type of die cutting has a process suitable for low-cut material conversion applications, but the lead time is fast and therefore low cost still provides high accuracy.
4. Components for die cutting
In order to have the right set of components for the types of die cutting processes to be performed, most of them use a variety of die cutters and die cutters to create cuts, designs and parts.
Flat die cutting process will use a flat die cutting press and steel rule stamping die. Often they will be available in mechanical, hydraulic and electrical models with system configurations varying based on the specific installed cutting application. About a steel rule stamping die includes a custom-designed steel rule, which has cutting elements of the die and die base, including those that hold the steel rule in place and maintain its shape. In addition, there are several types of steel rule molds available including billet die, combination die, progressive die and progressive feed die.
The rotary die cutting process will have to use a rotary die press and a cylindrical die designed specifically for it. At the same time, the rotary press uses both flexible and solid cylindrical rotary dies, also depending on the material to be cut, along with the specifications, including the limitation of investment costs and production time. product as originally requested.
The digital die cutting process will use computer controls to perform and operate knives, blades and related machine tools. Often the required design information for parts is digitally transmitted to the cutting mechanism to produce the cuts, holes, scores, and creases produced.
5. Suitable materials for die cutting
The die cutting process is suitable for a wide range of materials including metal, plastic, paper, fabric, foam, wood and composites. Virtually the converted material and its properties will in part determine the die cutting processes to use for the application, as well as the overall machine configuration and optimal die design.
The flat die cutting process can convert materials in both sheet and roll form. Most material properties are the thickness and compressive strength of the material as they can affect the design and shape of the die, including the suitability of using the flat die cutting process for the parts. certain die cutting applications. Because they are capable of generating high cutting pressure and are very suitable for cutting through soft and thin materials, as well as hard and thick materials.
The rotary die cutting process is capable of transforming web materials. Similar to the flat die cutting process, the way they cut through also affects the rotary die design and the cutting pressure caused by the rotary press. The properties of the material also contribute to the selection of a suitable plastic or solid mold.
The digital die-cutting process will suit a wide variety of materials including textiles, paper to plastic. However, they are capable of processing low-cut materials similar to flat or rotary die cutting. Very suitable for processing materials with high shear, and for the most part the lead time is much longer.
6. Different types of cutting
Cutting is a process of making and using a variety of molds designed, then attached to specialized machinery to convert raw materials. And it is truly suitable for a wide range of materials and applications with different industries. Besides, the die-cutting process still offers several different cutting operation possibilities such as through-cutting, kiss-cutting, punching, scoring, creasing.
Through cutting is known as metal to metal die cutting or through cutting, through cutting cuts the custom design through the entire material. When the plastic cutter has a non-stick coating, the molds will cut through the layers of the substrate, the adhesive layer, and the plastic surface. This type of design is completely separated from the original materials.
Kiss cutting is known for adhesive lined material, the cut allows custom design cut kiss cuts through face layers and adhesive layers, but not through base material cuts. The mold design will not be separated from the parent material but is easily separated from the base layer.
Perforating will create holes to hold the die cut design on the fixed surface of the parent materials. And the design will not completely separate from the materials but easily separate along the perforated lines.
Scoring is known to not completely cut the parent material, but rather to leave marks, dents or partial cuts at one point. And the points created are usually only through the cuts in half of the material, which in turn reduces the thicknesses at the stress point, allowing for the formation of square folds.
7. Let's have a look on a very cool Cricut product die cutting
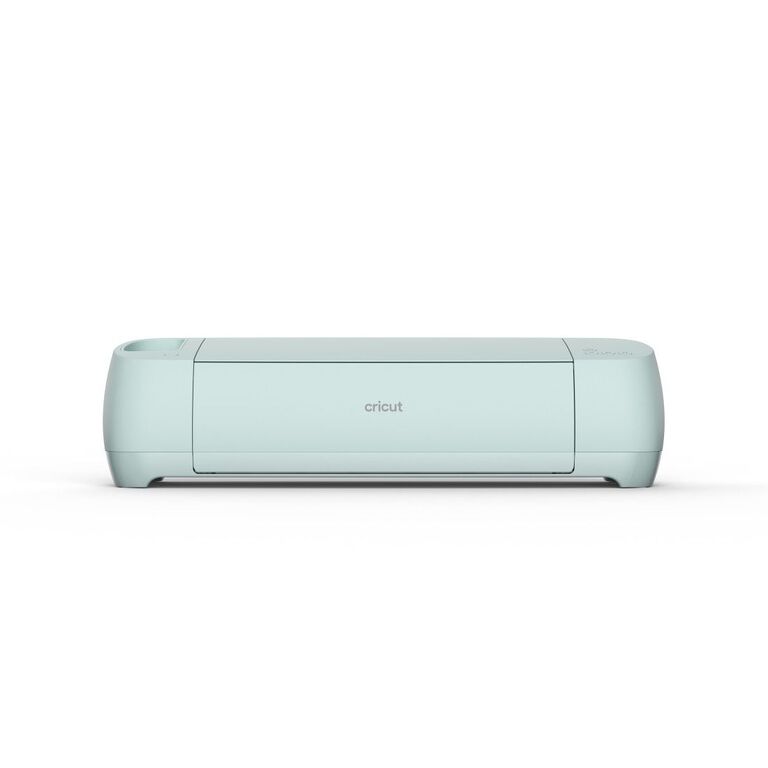
With Cricut's original purpose of helping people to work creatively through the use of products we provide tools to make user work schedules convenient in modern life today. And when we came up with the concept of building the first cutting machine, a vision of a simple tool with the potential to completely change the way people think about manufacturing and design.
This helps Cricut continuously innovate the way it looks and create new machines, materials and tools that give meaning and uniqueness to the user. Along with a team of enthusiastic employees in creative work, we believe that we will always update and change to be more suitable for consumers.
Here is one of the products that we would like to introduce to you. Cricut Explore® 3 is used for cutting, drawing, scoring, with high speed and precision. The Cricut Explore 3 is similar to the Cricut Smart Materials™ because they cut easily, super long up to 12 ft (3. 6 m) without the need for an additional machine mat.
Besides, they can work with six different tools at the same time to cut and decorate 100s of materials, including cardboard, vinyl, iron top, glitter paper, cork and bonded fabric. The blade part, on the other hand, is considered a smooth cut, combined with the foil transfer tool to provide additional second-degree foil decorations. They feature a combination of a marker pen and a deep-cut blade. In addition, the movement has Bluetooth wireless connectivity and slots for mobile devices and built-in memory.
Conclusion
Here's the basics of the die-cutting process, the different types of die-cutting dies, and the equipment needed for a die-cutting machine. Note that die cutting machines can have many forms and also depending on the purpose of each individual use, they will work in many different forms.
Usually rotary die cutting and laser die cutting are the two main processes used by most printing companies. And industrial-style die-cutting machines are very expensive and are capable of creating eye-catching custom die cuts quickly.
In contrast, manual die-cutting machines are for individuals and craft items. In fact, rotary die cutters have to be customized to cut through the substrate. From there the rotary dies can produce various cuts. That's the information we want to send you. Below are some product links you can refer to to choose for yourself a good product. Thanks for reading my reviews.